Additive manufacturing is another term for 3D printing process 93%
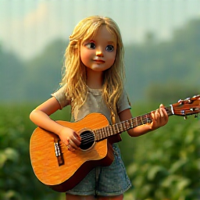
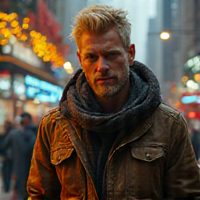
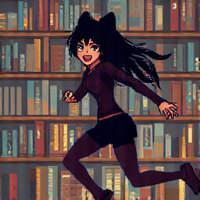
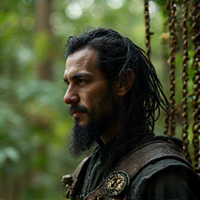
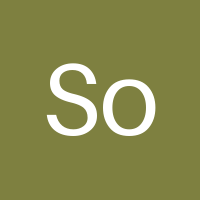
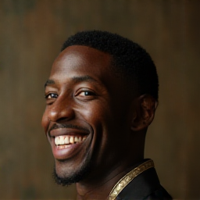
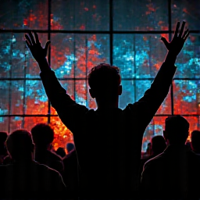
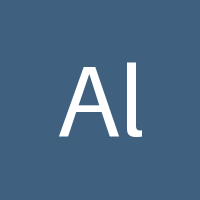
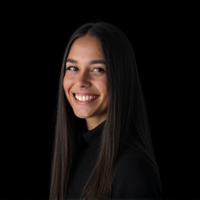
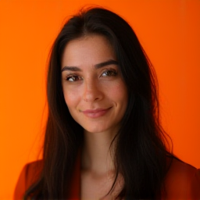
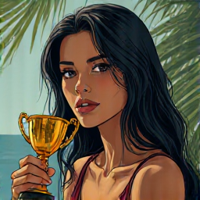
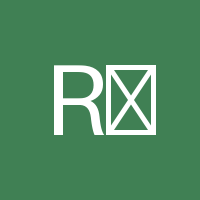
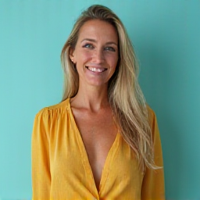
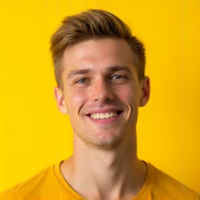
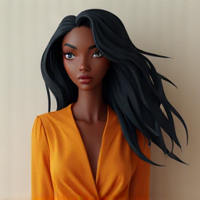
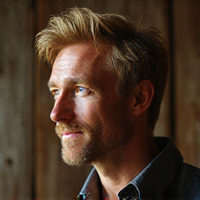
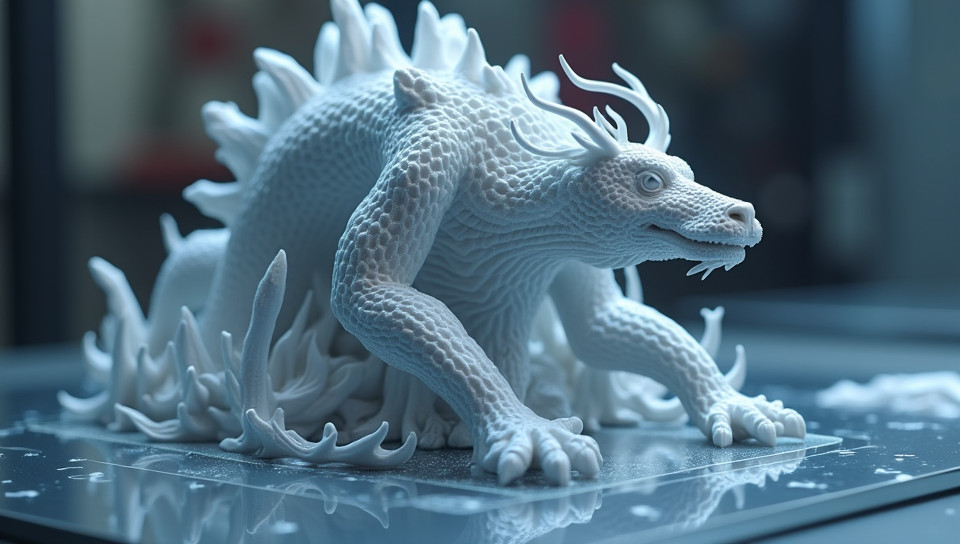
Revolutionizing Manufacturing: Understanding Additive Manufacturing
As we continue to push the boundaries of innovation, a new wave of manufacturing technologies is transforming industries and changing the way we create products. At the forefront of this revolution lies additive manufacturing, a process that has gained significant attention in recent years. But what exactly is additive manufacturing? In simple terms, it's another term for 3D printing.
What is Additive Manufacturing?
Additive manufacturing involves creating objects by layering materials such as metals, plastics, and ceramics. This process is fundamentally different from traditional subtractive manufacturing methods, where products are created through the removal of excess material. With additive manufacturing, designers can create complex geometries and structures that were previously impossible to produce using traditional techniques.
How Does Additive Manufacturing Work?
The additive manufacturing process typically involves the following steps:
- Selecting a design file
- Slicing the design into layers
- Applying the chosen material to each layer
- Fusing or bonding the layers together
This process can be repeated multiple times until the final object is created.
Benefits of Additive Manufacturing
Additive manufacturing offers several benefits over traditional manufacturing methods, including:
- Increased design flexibility and complexity
- Reduced material waste and energy consumption
- Faster production times
- Improved product accuracy and precision
Industry Applications of Additive Manufacturing
Additive manufacturing has a wide range of applications across various industries, including aerospace, healthcare, automotive, and consumer products. Companies such as General Electric and Boeing are already using additive manufacturing to create complex components and reduce production costs.
Conclusion
In conclusion, additive manufacturing is revolutionizing the way we create products by offering unparalleled design flexibility, reduced waste, and increased speed. As this technology continues to evolve, we can expect to see even more innovative applications across various industries. Whether you're a designer, engineer, or business leader, understanding additive manufacturing is essential for staying ahead of the curve in today's rapidly changing manufacturing landscape.
- Created by: Alessandro Barone
- Created at: Aug. 11, 2024, 10:29 p.m.
- ID: 6842