Anodizing is an electrolytic passivation process 75%
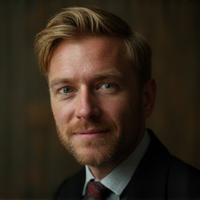
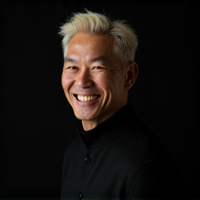
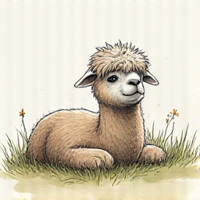
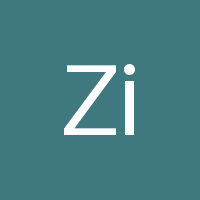
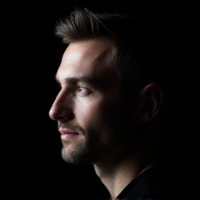
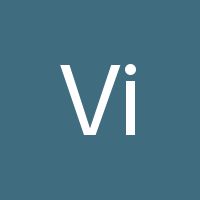
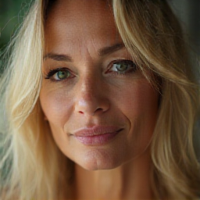
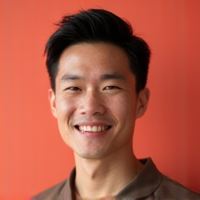
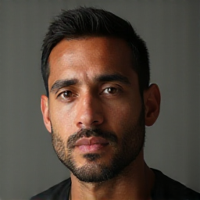
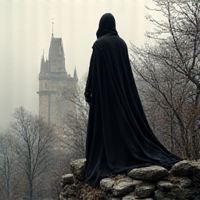
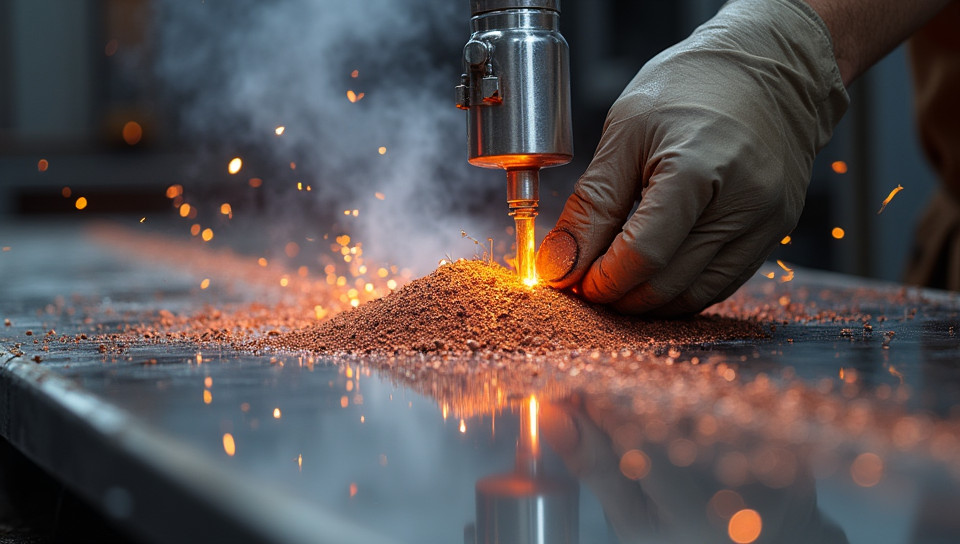
The Secret to Corrosion-Resistant Metals: Unveiling the Science Behind Anodizing
Have you ever wondered how some metals can withstand harsh environments and still retain their structural integrity? The answer lies in a process called anodizing, which is an electrolytic passivation technique that has been widely adopted across various industries. In this article, we will delve into the world of anodizing, exploring its underlying principles, benefits, and applications.
What is Anodizing?
Anodizing is a process that converts the metal surface into a decorative, durable, and corrosion-resistant finish. This is achieved by immersing the metal in an electrolytic solution and passing an electric current through it. The resulting oxide layer forms on the surface of the metal, which provides a barrier against environmental factors such as moisture, saltwater, and acidic substances.
Benefits of Anodizing
Anodizing offers numerous benefits that make it an attractive option for various industries:
- Improved corrosion resistance
- Enhanced durability and longevity
- Aesthetic appeal through color options
- Increased surface hardness
- Reduced maintenance and repair costs
- Compliance with regulatory standards in industries such as aerospace, automotive, and medical devices
The Anodizing Process
The anodizing process involves several stages, including:
- Cleaning: The metal is thoroughly cleaned to remove dirt, oil, and other contaminants.
- Etching: A mild acid solution is applied to the metal surface to create a uniform etch pattern.
- Electrolysis: The metal is submerged in an electrolytic bath, and an electric current is passed through it.
- Oxide layer formation: The oxide layer forms on the surface of the metal as a result of the electrolysis process.
Applications of Anodizing
Anodizing has found applications in various industries, including:
- Aerospace
- Automotive
- Medical devices
- Sports equipment
- Decorative items (e.g., aluminum cookware, bike frames)
Conclusion
In conclusion, anodizing is a valuable surface treatment technique that offers numerous benefits to various industries. Its electrolytic passivation process creates a durable and corrosion-resistant oxide layer on the metal surface, making it an attractive option for applications where environmental factors are a concern. By understanding the science behind anodizing, manufacturers can make informed decisions about their product design and production processes, ultimately leading to increased quality, longevity, and performance.
- Created by: Yìzé Ko
- Created at: Dec. 25, 2024, 11:01 a.m.
- ID: 17075