Fused deposition modeling is a widely used 3D printing technology 84%
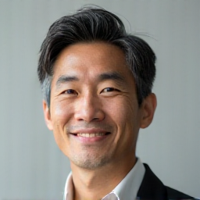
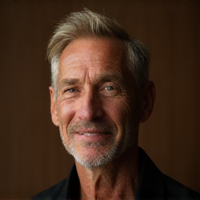
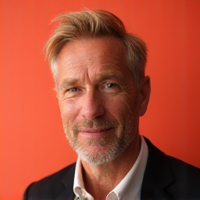
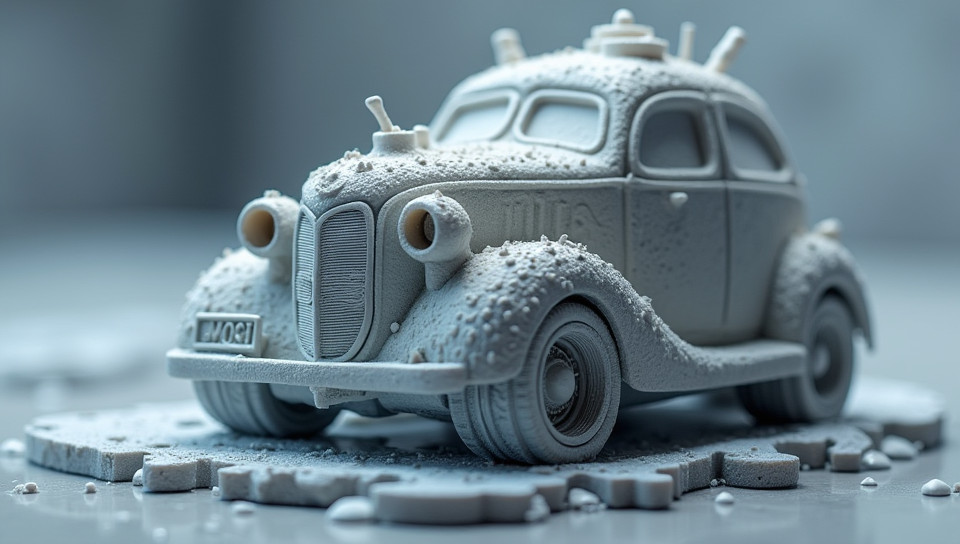
The Future of Manufacturing: Understanding Fused Deposition Modeling
Imagine being able to create complex objects layer by layer, without the need for traditional manufacturing methods like injection molding or casting. Sounds like science fiction, right? But with the rise of 3D printing technologies, this is now a reality. One such technology that has gained immense popularity in recent years is Fused Deposition Modeling (FDM). In this article, we'll delve into the world of FDM and explore its benefits, applications, and limitations.
What is Fused Deposition Modeling?
Fused Deposition Modeling is an additive manufacturing process where a plastic filament is melted and extruded through a heated nozzle to create a 3D object. The process starts with a computer-aided design (CAD) model of the object, which is sliced into layers by a slicing software. The 3D printer then reads these layer files and begins printing the object one layer at a time.
Benefits of FDM
Fused Deposition Modeling offers several benefits over traditional manufacturing methods, including: - - Cost-effectiveness - - Flexibility in design - - Reduced material waste - - Rapid prototyping capabilities
Applications of FDM
The applications of FDM are vast and diverse. Some of the most common uses include:
- Creating prototypes for product testing and validation
- Producing end-use parts such as phone cases, bike helmets, and tool handles
- Creating medical models for surgical planning and training
- Developing educational aids like 3D models and simulations
Limitations of FDM
While FDM is a powerful technology, it's not without its limitations. Some of the challenges associated with FDM include:
- Limited material options compared to traditional manufacturing methods
- Inconsistent layer adhesion leading to defects in the finished product
- Long printing times for complex objects
Conclusion
Fused Deposition Modeling has revolutionized the way we manufacture and design products. Its flexibility, cost-effectiveness, and rapid prototyping capabilities make it an attractive option for industries ranging from healthcare to education. While there are limitations to FDM, advancements in technology and innovation are continually pushing the boundaries of what's possible. As 3D printing continues to grow in popularity, we can expect to see even more exciting applications of FDM in the years to come.
- Created by: Sōma Nishimura
- Created at: Aug. 11, 2024, 10:14 p.m.
- ID: 6832