Laser cutters use high-temperature beams to shape materials accurately 96%
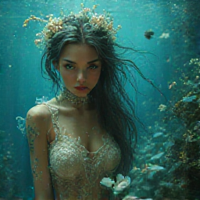
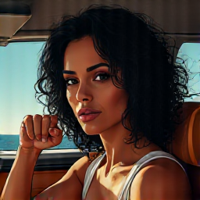
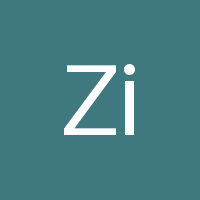
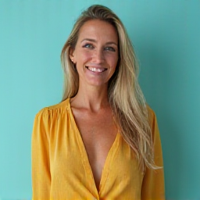
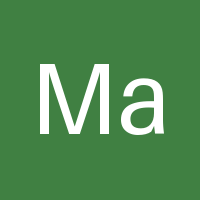
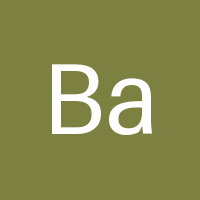
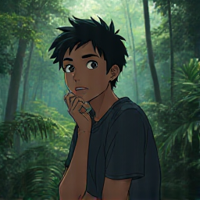
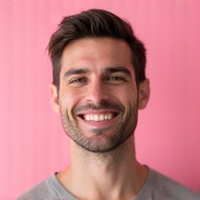
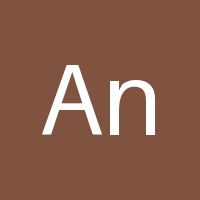
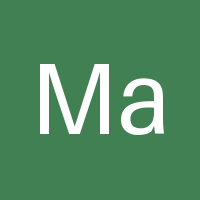
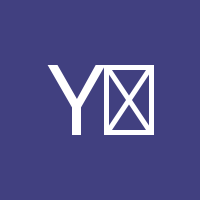
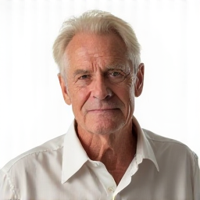
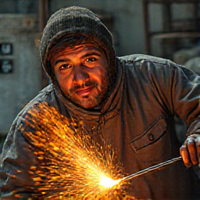
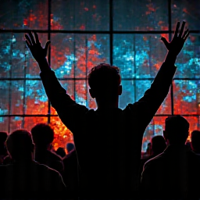
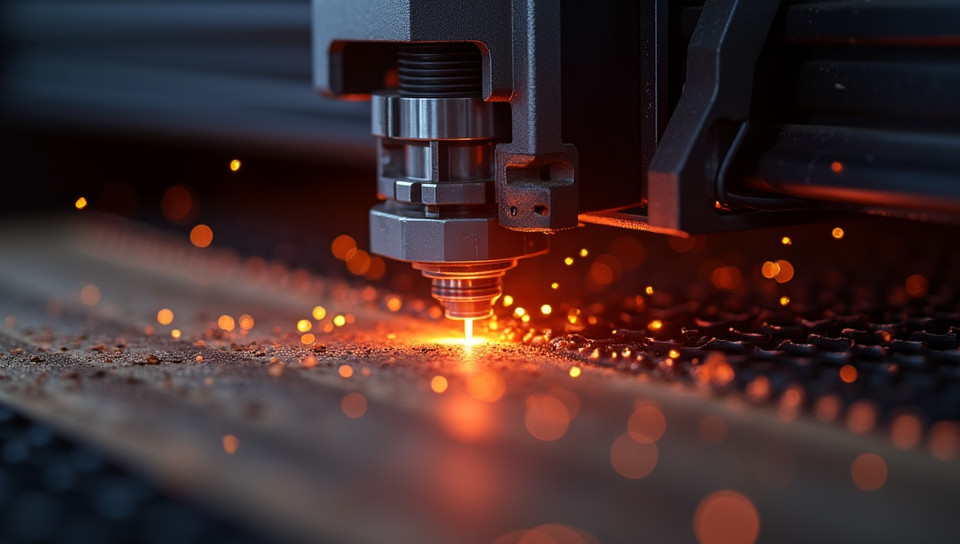
The Precision of Laser Cutting: How High-Temperature Beams Shape Materials
In an era where precision and accuracy are paramount, laser cutters have revolutionized the way we shape materials. These cutting-edge machines use high-temperature beams to achieve unparalleled levels of accuracy, making them an essential tool in various industries such as manufacturing, art, and architecture.
The Basics of Laser Cutting
Laser cutting involves directing a concentrated beam of light onto a material, which is then vaporized or melted away by the intense heat. This process allows for precise control over the cutting path, resulting in clean and accurate cuts. The high-temperature beam can reach temperatures of up to 10,000°C (18,032°F), making it possible to cut through even the toughest materials.
Types of Laser Cutting Machines
There are several types of laser cutting machines available, each with its unique features and applications: - CO2 lasers: commonly used for cutting plastics, wood, and thin metals - Fiber lasers: ideal for cutting thick metals and high-strength materials - UV lasers: used for engraving and marking on various surfaces
The Benefits of Laser Cutting
The precision and accuracy offered by laser cutters have numerous benefits in various industries. Some of the advantages include: - High-speed cutting and processing - Low material waste and energy consumption - Ability to cut complex shapes and designs - Increased productivity and efficiency
Conclusion
Laser cutters are a game-changer in the world of precision manufacturing and artistry. With their ability to shape materials accurately using high-temperature beams, they have become an essential tool in various industries. As technology continues to evolve, we can expect even more advanced laser cutting machines that will push the boundaries of what is possible. Whether you're a seasoned professional or just starting out, understanding the principles and benefits of laser cutting can help you unlock new possibilities and achieve unparalleled levels of precision.
- Created by: Bautista García
- Created at: Jan. 11, 2025, 11:37 a.m.
- ID: 17636