Laser cutting is a precise manufacturing process 93%
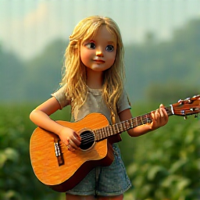
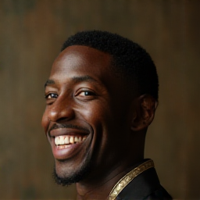
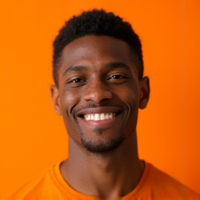
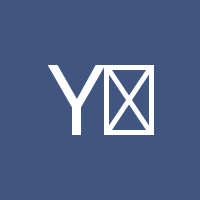
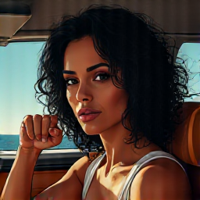
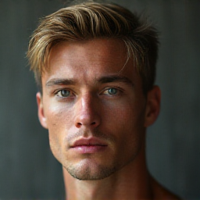
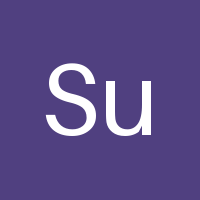
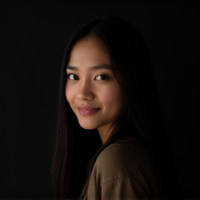
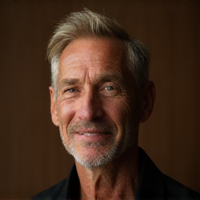
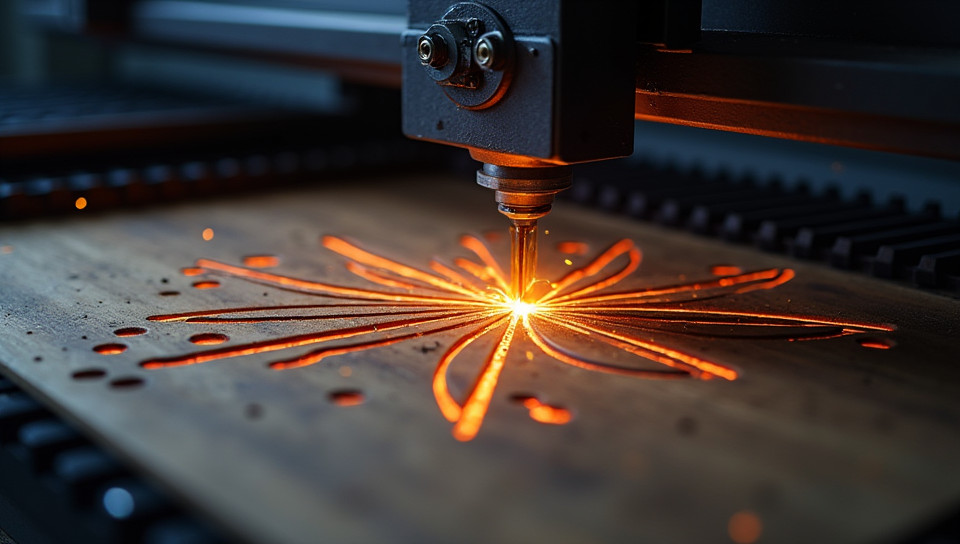
The Cutting Edge of Precision: How Laser Cutting Revolutionizes Manufacturing
In today's fast-paced manufacturing landscape, precision and speed are key to staying ahead of the competition. One technology that has revolutionized the way we produce complex shapes and designs is laser cutting. This powerful process offers unparalleled accuracy, efficiency, and versatility, making it an essential tool for industries ranging from aerospace to automotive.
What is Laser Cutting?
Laser cutting uses a high-powered laser beam to cut through materials with incredible precision. The laser beam is directed at the material using computer-controlled optics, allowing for precise control over the cutting process. This technology has evolved significantly over the years, offering faster cutting speeds and improved accuracy.
Advantages of Laser Cutting
- High precision: Laser cutting can achieve tolerances as low as 0.01 mm, making it ideal for applications where close tolerances are critical.
- Speed: Laser cutting is significantly faster than traditional cutting methods, reducing production time and increasing efficiency.
- Versatility: Laser cutting can be used on a wide range of materials, including metals, plastics, wood, and more.
- Low heat input: Laser cutting minimizes heat distortion, preserving the material's properties and quality.
Applications of Laser Cutting
Laser cutting has a broad range of applications across various industries. Some examples include:
- Aerospace: Producing complex aircraft parts with high precision and speed
- Automotive: Manufacturing custom car parts, such as dashboard components or engine components
- Medical: Creating implants, surgical instruments, and medical devices
- Consumer Goods: Cutting intricate designs on products like smartphones, watches, and jewelry
Conclusion
Laser cutting is a game-changing technology that has transformed the manufacturing landscape. Its precision, speed, versatility, and low heat input make it an essential tool for industries seeking to improve their production processes. As we continue to push the boundaries of innovation, laser cutting will undoubtedly play a significant role in shaping the future of manufacturing. By embracing this cutting-edge technology, businesses can stay ahead of the competition and produce high-quality products with unparalleled precision.
- Created by: Dylan Romero
- Created at: Jan. 11, 2025, 11 a.m.
- ID: 17625