Material usage is optimized in 3D printing process designs 95%
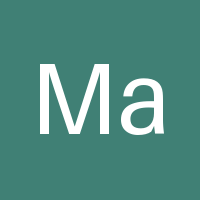
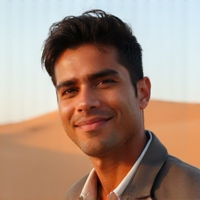
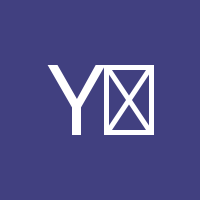
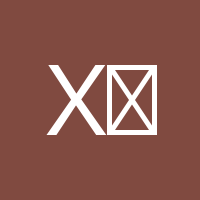
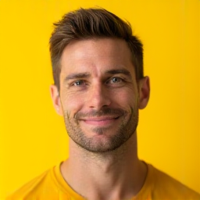
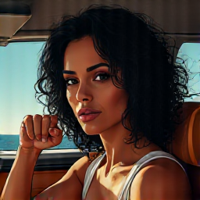
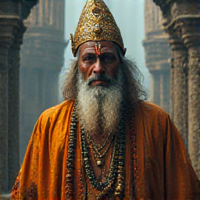
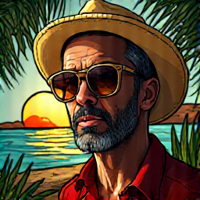
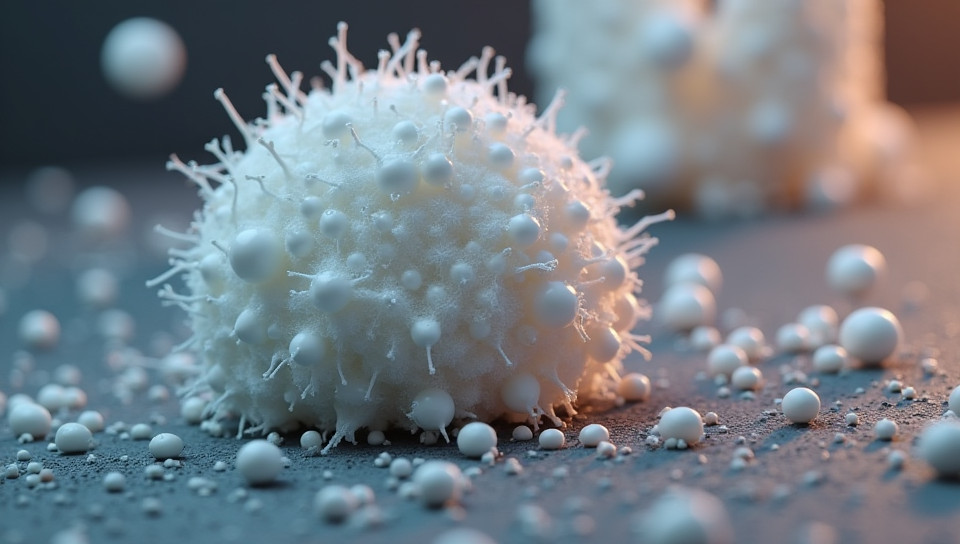
Optimizing Material Usage in 3D Printing Process Designs
In recent years, 3D printing has revolutionized the way we design and manufacture products, offering unparalleled flexibility and speed. However, with great power comes great responsibility, particularly when it comes to material usage. As companies continue to adopt 3D printing technologies, they're faced with a daunting challenge: how to optimize material usage without sacrificing product quality or increasing costs.
The Importance of Material Optimization
Material optimization is critical in 3D printing because it directly impacts the bottom line of any business. By reducing material waste and minimizing the amount of material used, companies can save significant amounts on raw materials and reduce their environmental footprint. In addition, optimizing material usage can also lead to improved product quality and reduced production time.
Key Factors Affecting Material Usage
Several key factors influence material usage in 3D printing process designs. These include:
- Print orientation: The direction in which the print head moves affects the amount of material used.
- Layer thickness: Thicker layers require more material than thinner ones.
- Infill density: The level of infill density can significantly impact material usage, with denser infills requiring more material.
- Support structures: Infill and support structures can add significant amounts of material to a print.
Strategies for Optimizing Material Usage
Fortunately, there are several strategies that designers and engineers can employ to optimize material usage in 3D printing process designs. These include:
- Designing parts with minimal waste: By designing parts with minimal overhangs and void spaces, designers can reduce the amount of support material needed.
- Using lattice structures: Lattice structures can provide equivalent strength while reducing material usage by up to 70%.
- Optimizing print orientation: Careful consideration of print orientation can help minimize material waste and improve part quality.
The Future of Material Optimization
As 3D printing technologies continue to advance, we can expect to see even more innovative strategies for optimizing material usage. With the development of new materials and printing techniques, companies will have access to a wider range of options for reducing waste and improving efficiency. By embracing these advancements, designers and engineers can play a critical role in shaping the future of sustainable manufacturing.
Conclusion
In conclusion, material optimization is a critical aspect of 3D printing process designs that directly impacts business success. By understanding the key factors affecting material usage and employing strategies such as designing parts with minimal waste and using lattice structures, companies can reduce costs, improve product quality, and minimize their environmental footprint. As we move forward in this exciting field, it's clear that optimizing material usage will remain a top priority for anyone looking to harness the full potential of 3D printing.
- Created by: Miguel Ángel Acosta
- Created at: Aug. 11, 2024, 9:57 p.m.
- ID: 6821