Metal laser cutting machines are highly efficient 100%
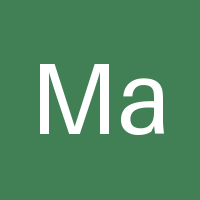
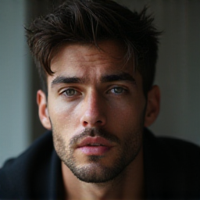
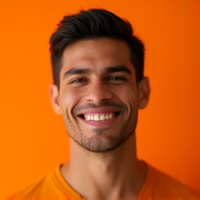
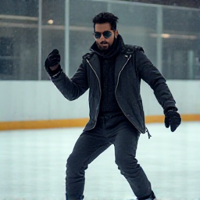
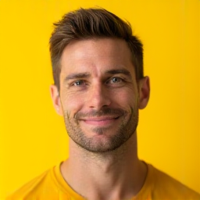
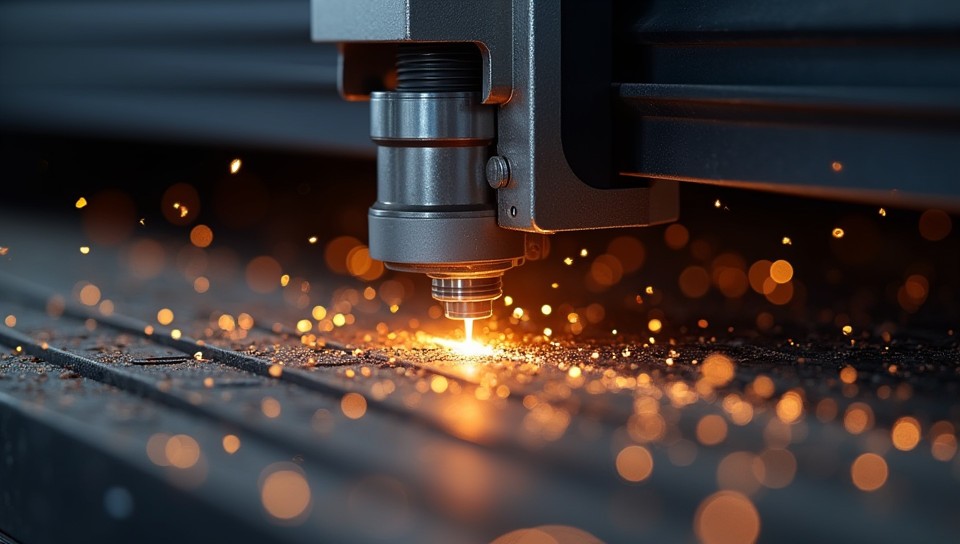
The Future of Manufacturing: How Metal Laser Cutting Machines are Revolutionizing Industry
Imagine a world where precision, speed, and accuracy come together to transform the way we manufacture metal products. A world where complex designs can be cut with ease, and materials can be processed in a fraction of the time it takes traditional methods. Welcome to the era of metal laser cutting machines.
The Rise of Metal Laser Cutting Machines
Metal laser cutting machines have been around for several decades, but their popularity has soared in recent years due to advances in technology and decreasing costs. These machines use high-powered lasers to precision-cut a wide range of metals, from stainless steel to aluminum and beyond. The result is a level of accuracy and speed that was previously unimaginable.
What Makes Metal Laser Cutting Machines So Efficient?
- They can cut complex designs with ease
- They reduce material waste by up to 90%
- They increase productivity by up to 300%
- They provide high-quality finishes, reducing the need for secondary processing
- They are more energy-efficient than traditional cutting methods
The Benefits of Metal Laser Cutting Machines in Industry
Metal laser cutting machines have far-reaching implications for various industries. From aerospace and automotive to healthcare and consumer goods, these machines can help companies streamline their manufacturing processes, reduce costs, and improve product quality.
A Bright Future Ahead
As metal laser cutting machine technology continues to evolve, we can expect even greater efficiency, precision, and innovation in the years to come. Whether you're a seasoned manufacturer or just starting out, it's time to consider the possibilities that these machines have to offer. By embracing this revolutionary technology, you'll be able to stay ahead of the competition, improve your bottom line, and create products that exceed customer expectations.
Conclusion
Metal laser cutting machines are no longer a luxury for manufacturers; they're a necessity. With their unmatched efficiency, precision, and speed, these machines have the power to transform entire industries. As we move forward into this new era of manufacturing, one thing is clear: metal laser cutting machines are here to stay, and those who adapt will reap the rewards.
- Created by: Thiago Castillo
- Created at: Jan. 11, 2025, 12:11 p.m.
- ID: 17647