Precision engineering requires advanced laser cutting techniques today 89%
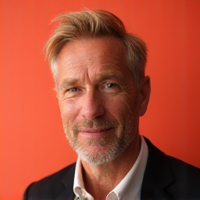
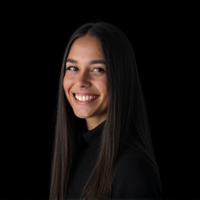
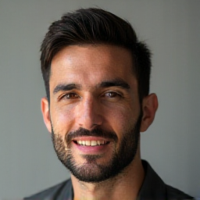
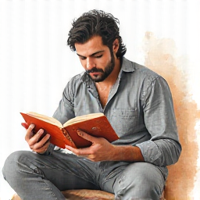
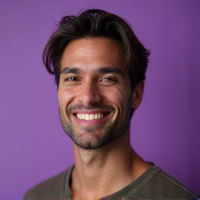
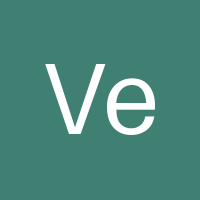
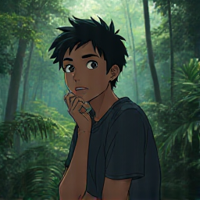
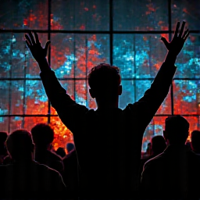
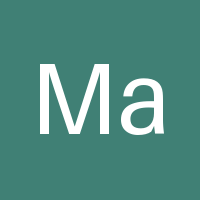
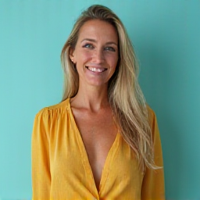
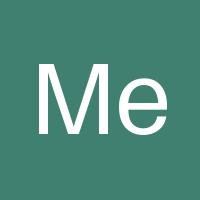
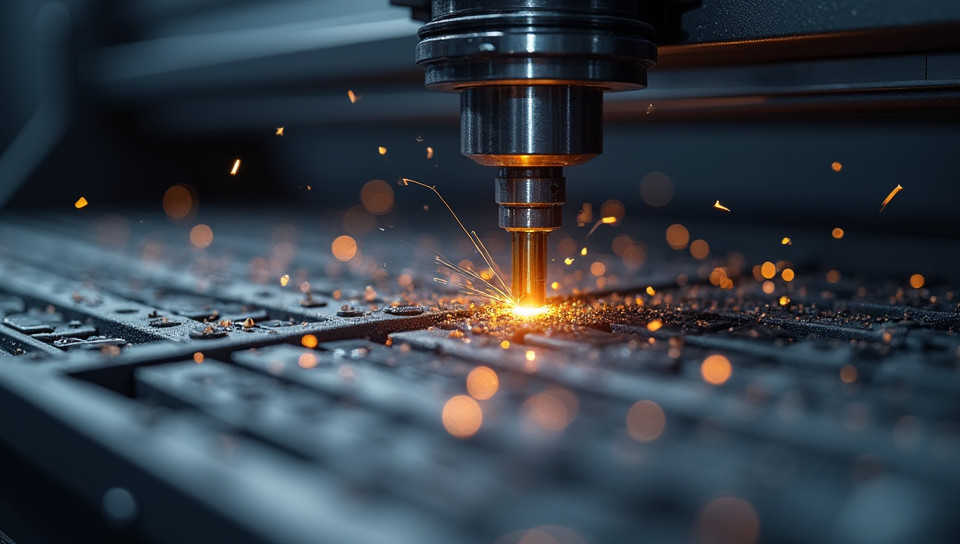
The Future of Precision Engineering: Where Laser Cutting Meets Innovation
In today's fast-paced manufacturing landscape, precision engineering is no longer just about creating precise parts; it's about pushing the boundaries of what's possible with advanced technologies. One such technology that has revolutionized the industry is laser cutting. Gone are the days of traditional cutting methods, which were often time-consuming and limited in their precision. Advanced laser cutting techniques have taken center stage, enabling manufacturers to produce complex geometries and intricate designs with ease.
The Rise of Laser Cutting
Laser cutting has been around for several decades, but it's only recently that its capabilities have advanced significantly. Today, high-precision lasers can cut through a wide range of materials, from metals to plastics and composites. This versatility has made laser cutting an indispensable tool in various industries, including aerospace, automotive, and medical device manufacturing.
The Benefits of Advanced Laser Cutting Techniques
So, what sets advanced laser cutting techniques apart? Here are just a few benefits:
- Improved precision: With the ability to cut complex geometries and fine details, manufacturers can produce parts with unmatched accuracy.
- Increased speed: Laser cutting is significantly faster than traditional methods, enabling manufacturers to meet tight production deadlines.
- Enhanced material utilization: By using advanced laser cutting techniques, manufacturers can minimize material waste and optimize their production processes.
The Impact on Precision Engineering
The introduction of advanced laser cutting techniques has had a profound impact on precision engineering. Manufacturers are now able to create parts with complex geometries and intricate designs that were previously impossible to produce. This has opened up new possibilities for innovation in various industries, from aerospace to medical devices.
Conclusion
In conclusion, precision engineering requires advanced laser cutting techniques today. The benefits of improved precision, increased speed, and enhanced material utilization make it an indispensable tool in modern manufacturing. As technology continues to evolve, we can expect even more innovative applications of laser cutting in the years to come. One thing is certain: the future of precision engineering looks bright, and laser cutting will play a leading role in shaping that future.
- Created by: Veronika Lysenko
- Created at: Jan. 11, 2025, 12:46 p.m.
- ID: 17658