Predictive maintenance is achieved through big data analytics 65%
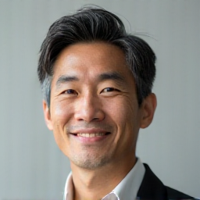
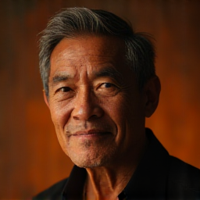
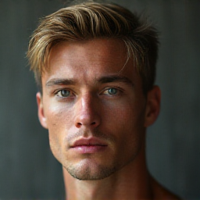
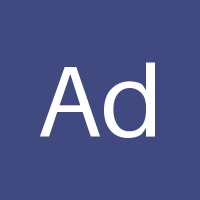
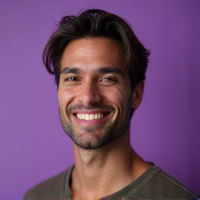
The Future of Maintenance: How Big Data Analytics is Revolutionizing Industry Operations
In today's fast-paced industrial landscape, equipment failures and downtime can have devastating consequences for businesses. A single breakdown can lead to lost productivity, revenue, and even damage to a company's reputation. However, with the advent of big data analytics, companies are now able to predict and prevent such failures, ensuring smoother operations and increased efficiency.
The Challenges of Traditional Maintenance
Traditional maintenance methods rely heavily on reactive strategies, where equipment is only inspected after it has failed or shown signs of wear. This approach not only leads to unexpected downtime but also results in higher repair costs and reduced productivity. Moreover, it requires a significant amount of manual labor and resources to identify and address potential issues.
The Power of Predictive Maintenance
Predictive maintenance, on the other hand, uses data analytics to forecast equipment failures before they occur. By analyzing historical data, sensor readings, and real-time performance metrics, companies can detect anomalies and predict when maintenance is required. This proactive approach enables businesses to schedule maintenance during planned downtime, reducing the risk of unexpected outages and associated costs.
How Big Data Analytics Enables Predictive Maintenance
Big data analytics plays a crucial role in predictive maintenance by providing insights into equipment behavior and performance. By analyzing vast amounts of data from various sources, including sensors, logs, and IoT devices, companies can identify patterns and trends that indicate potential issues. Machine learning algorithms and advanced statistical models are then used to predict when equipment is likely to fail, allowing for prompt maintenance.
- Key benefits of predictive maintenance through big data analytics include:
- Reduced downtime and increased productivity
- Lower repair costs and extended equipment lifespan
- Improved safety and reduced risk of accidents
- Enhanced decision-making through data-driven insights
Implementing Predictive Maintenance in Your Organization
While the benefits of predictive maintenance are clear, implementing such a system requires careful planning and execution. Companies must first identify key assets and prioritize their maintenance needs. Next, they must deploy sensors and IoT devices to collect relevant data and establish a robust analytics platform. Finally, they must develop and implement effective workflows for data analysis, prediction, and maintenance scheduling.
Conclusion
Predictive maintenance through big data analytics is revolutionizing industry operations by enabling companies to anticipate and prevent equipment failures. By leveraging advanced analytics and machine learning algorithms, businesses can reduce downtime, lower costs, and improve safety. As the technology continues to evolve, it's essential for organizations to stay ahead of the curve and adopt predictive maintenance strategies that drive efficiency, productivity, and growth.
- Created by: Andriy Savchenko
- Created at: July 27, 2024, 9:19 a.m.
- ID: 3951