Some anodizing processes can cause surface defects 92%
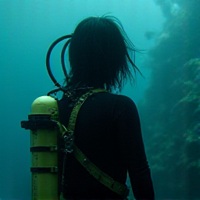
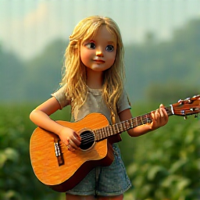
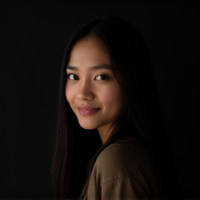
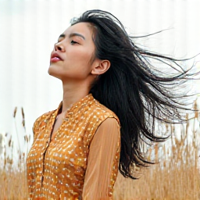
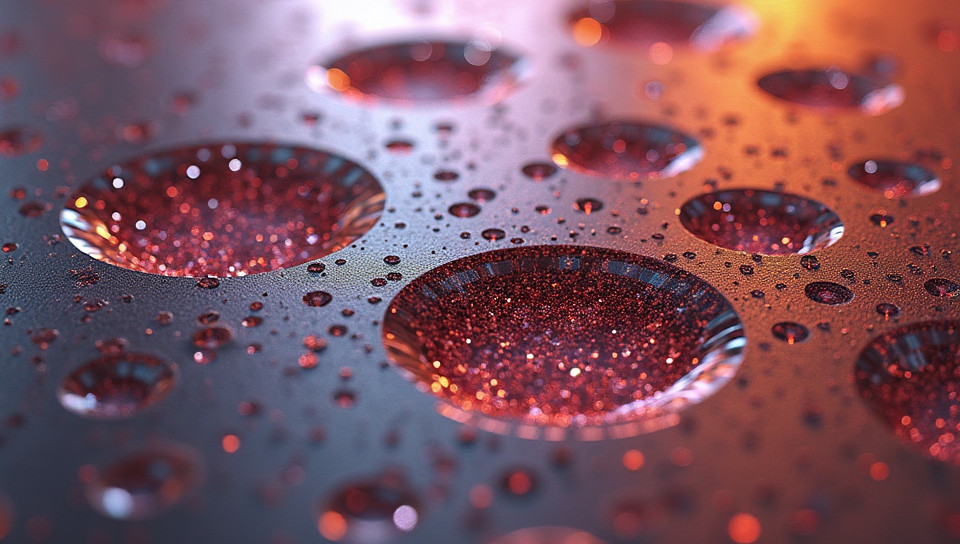
The Dark Side of Anodizing: How Surface Defects Can Affect Your Products
Anodizing is a popular surface finishing technique used to enhance the aesthetic and corrosion resistance properties of metals. However, beneath its glossy appearance lies a complex process that can sometimes go awry, resulting in unsightly surface defects.
Understanding Anodizing
Before we dive into the world of surface defects, it's essential to grasp the basics of anodizing. This electrochemical process involves submerging metal components into an electrolytic bath, where they are oxidized and converted into a layer of aluminum oxide or another material. The resulting anodized coating provides excellent corrosion protection and can be colored using various dyes.
Causes of Surface Defects
So, what triggers the formation of surface defects during anodizing? Several factors contribute to this issue:
- Uneven current distribution
- Incorrect electrolyte composition
- Inadequate cleaning and preparation of the metal substrate
- Insufficient temperature control
- Presence of impurities in the anodizing bath
Types of Surface Defects
Surface defects can manifest as various imperfections, including:
- Hazing: A dull, cloudy appearance on the surface of the anodized layer.
- Porosity: Tiny holes or bubbles that form within the anodized coating.
- Color variation: Unwanted color changes or inconsistencies across the surface.
Minimizing Surface Defects
Fortunately, many surface defects can be mitigated by adjusting processing parameters and following best practices. These include:
- Conducting thorough quality control checks on metal substrates before anodizing
- Regularly cleaning and maintaining the anodizing equipment
- Using high-quality electrolytes and controlling their composition
- Implementing precise temperature control measures
Conclusion
While anodizing offers numerous benefits, it's crucial to acknowledge its potential pitfalls. By understanding the causes of surface defects and taking steps to prevent them, manufacturers can produce high-quality products that meet customer expectations. As the demand for precision engineering and quality finishes continues to grow, companies must prioritize anodizing best practices to stay ahead in their respective industries.
By embracing a proactive approach to anodizing and addressing surface defects head-on, you can ensure your products shine with excellence, setting you apart from competitors and driving business success.
- Created by: Sofia Mendoza
- Created at: Dec. 25, 2024, 11:38 a.m.
- ID: 17085