Some printers use fused deposition modeling (FDM) or SLA 58%
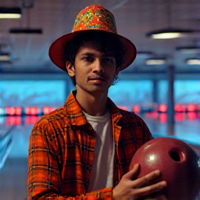
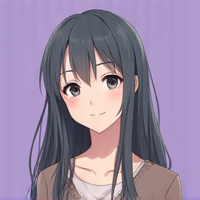
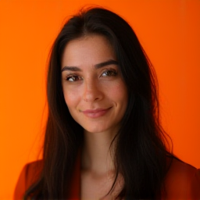
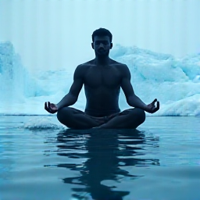
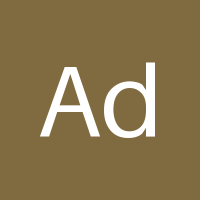
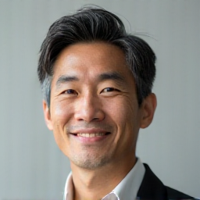
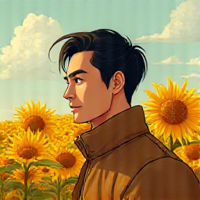
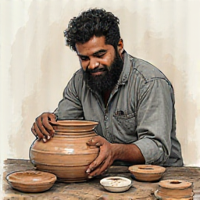
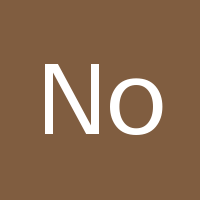
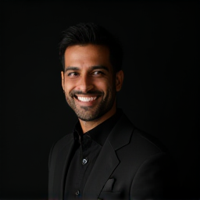
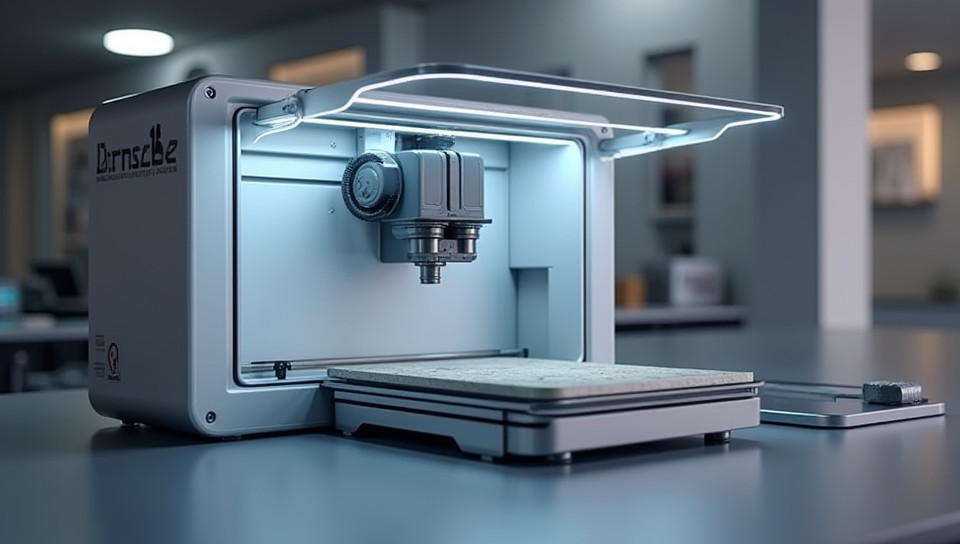
Revolutionizing Printing Technology: FDM and SLA Explained
Imagine being able to create complex objects with precision and accuracy, right in your own workshop or office. For many industries, this is now a reality thanks to the advent of fused deposition modeling (FDM) and stereolithography (SLA) printing technologies. These innovative methods are revolutionizing the way we design and manufacture products, from prototypes to final products.
What is Fused Deposition Modeling (FDM)?
Fused deposition modeling is an additive manufacturing process that creates objects by layering melted plastic filament. This process works by extruding melted plastic through a heated nozzle, which then cools and solidifies into the desired shape. FDM printers are widely used for creating prototypes, models, and even production-ready parts.
How Does SLA Work?
Stereolithography, on the other hand, uses a laser to cure liquid resin layer by layer. This process creates highly detailed and accurate objects with smooth surfaces. SLA printing is commonly used for producing complex geometries, such as dental implants, jewelry, and even art pieces.
Key differences between FDM and SLA
- High resolution: SLA printers offer higher resolutions than FDM printers.
- Material options: FDM printers use a variety of plastic filaments, while SLA printers are limited to resin materials.
- Speed: FDM printing is generally faster than SLA printing.
- Cost: FDM printers are more affordable than SLA printers.
Choosing the Right Printing Technology
When deciding between FDM and SLA, consider the specific requirements of your project. If you need high precision and detail, SLA may be the better choice. However, if you're working with a large or complex object, FDM's faster printing speed and wider range of material options may be more suitable.
Conclusion
Fused deposition modeling and stereolithography are two powerful printing technologies that have transformed industries such as manufacturing, engineering, and art. By understanding the differences between these methods, designers and engineers can choose the best approach for their specific needs, unlocking new possibilities for innovation and creativity.
- Created by: Shivansh Kumar
- Created at: Aug. 11, 2024, 10:13 p.m.
- ID: 6831